Pembuatan kaos merupakan salah satu wadah untuk produksi kaos yang memang dibutuhkan oleh kalangan masyarakat. Nah anda bisa memproduksi pakaian kaos sesuai dengan apa yang anda inginkan. Terlebih saat ini kaos memang menjadi salah satu jenis pakaian yang memang cukup banyak peminatnya. Bahkan kaos kini memang banyak dicari oleh beberapa kalangan karena kualitasnya yang bagus. Harga yang ditawarkan untuk pembuatan kaos ini memang terbilang sangat murah dan terjangkau untuk semua kalangan. Apalagi kaosini memang terbilang memiliki desain yang banyak tergantung selera masing-masing pengguna.
Proses Pembuatan Kaos.
Design / Sketch Dalam pembuatan baju, langkah pertama adalah membuat design atau sketsa. Yang melakukan tugas ini adalah designer. Seorang designer bertugas untuk merancang baju dan menuangkan kreativitasnya ke dalam kertas sketsa. Kemudian sketsa akan dianalisa oleh panel designer. Panel designer akan memilih beberapa design yang terbaik dan kemudian design tersebut akan diproses untuk dibuatkan pola. Berikut adalah proses pembuatan kaos:
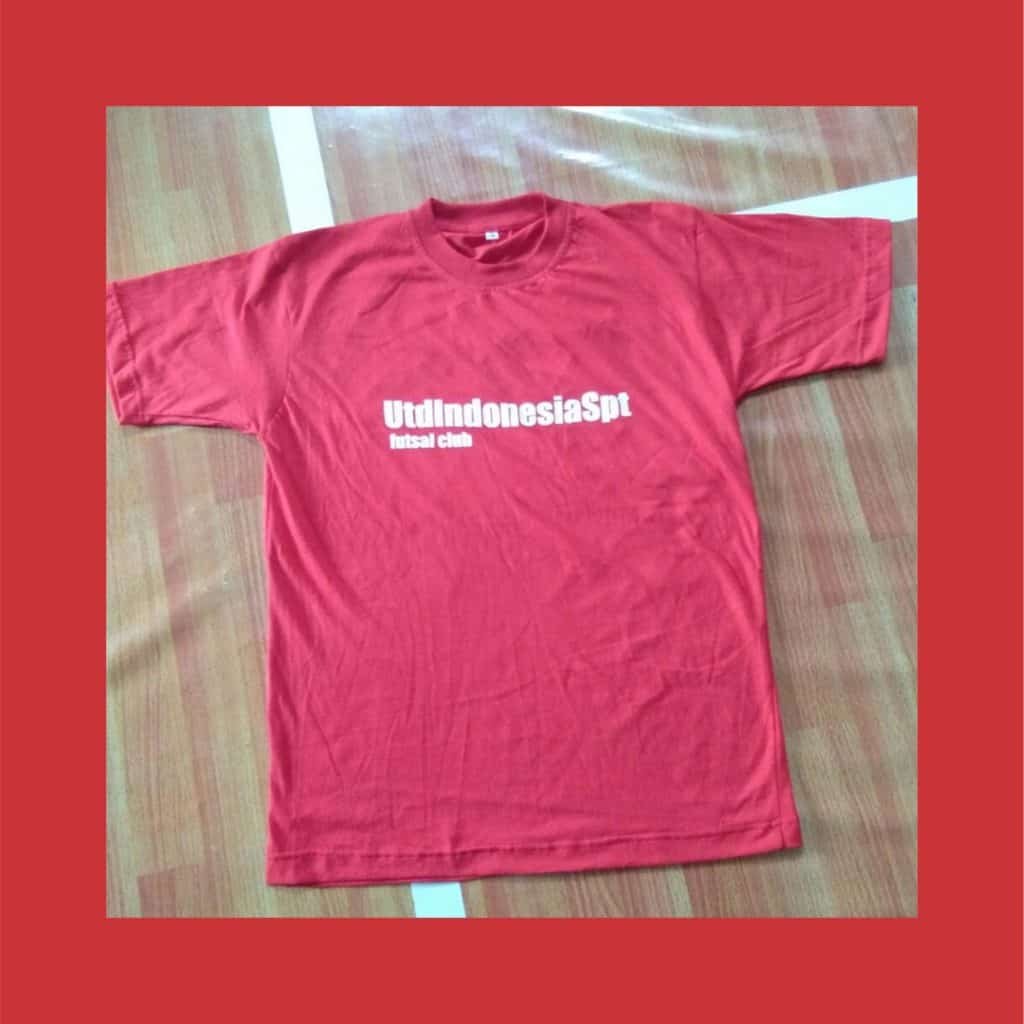
BACA JUGA : Tempat Pembuatan Kaos Terlengkap dan Termurah
Pemilihan Bahan atau Kain.
Tahap pertama dalam proses pembuatan kaos adalah pemilihan bahan kaos. Bahan kaos yang biasa digunakan adalah cotton. Ada beberapa jenis bahan cotton, yang sering digunakan untuk kaos kualitas distro adalah jenis cotton combed. Selain cotton ada pula jenis bahan polyster. Pemilihan bahan kaos bisa anda sesuaikan dengan kebutuhan atau bisa juga berdasarkan pemesanan.
Pemilihan Ukuran (grading).
Tujuan dari grading adalah untuk menciptakan pola dalam ukuran standar yang berbeda yaitu besar, sedang dan kecil atau ukuran standar lainnya. Dalam standar pola kaos terdapat ukuran S, M, L, dan XL. Ada juga ukuran free size untuk produksi massal. Pemilihan ukuran dilakukan sesuai dengan permintaan pelanggan.
Tahap Pemotongan Bahan atau Kain.
Proses pemotongan kain disebut juga cutting. Pemotongan kain kaos dilakukan dengan mesin cutting (mesin potong kain).
Sorting atau Bunding.
Menyortir pola sesuai dengan ukuran dan designnya dan kemudian tumpukan kain itu dibuat bundle. Pada proses ini membutuhkan ketelitian karena ketika kain dikumpulkan dalam bundle tapi ukuranya tidak sama, maka dapat membuat masalah yang lebih parah.
Tahap Penyablonan.
Setelah kain dipotong dan menjadi pola, tahap selanjutnya adalah penyablonan. Penyablonan bisa dilakukan di bagian khusus sablon. Penyablonan dilakukan menurut desain yang telah ditentukan pada awal pemesanan.
Sewing atau Penjahitan.
Setelah potongan pola kain kaos selesai disablon, tahap selanjutnya adalah penjahitan kain. Penjahitan dilakukan oleh bagian penjahitan. Tahap penjahitan kaos dilakukan dengan menggunakan beberapa mesin, antara lain mesin jahit, mesin obras, mesin overdeck, tergantung dari bagian kaos yang dijahit (penjahitan krah dalam, berbeda dengan penjahitan lengan, misalnya) dan jenis jahitan yang diingankan.
Finishing atau Quality Control.
Setelah tahap penjahitan kaos selesai dilakukan, tahap selanjutnya memasuki proses finishing. Pada tahap ini dilakukan pengecekan hasil produksi jahitan kaos, seperti membersihkan kaos, memotong dan merapikan benang, tahap pengecekan kualitas atau quality control, sehingga kaos yang lolos popses finishing ini adalah kaos yang benar-benar memiliki kualitas seperti yang diinginkan.
Packing.
Proses akhir dari produksi konveksi kaos adalah tahap pengemasan. Tahap ini bisa dilakukan dengan berbagai macam jenis kemasan. Kemasan plastik bening adalah kemasan yang banyak digunakan karena alasan kepraktisan dan ekonomis. Lalu kaos sudah siap untuk di kirim ke pemesan.
Baca Juga : Cara Mendapatkan Konveksi Murah Yang Berkualitas
Jika anda ingin mendapatkan jasa produksi kaos polos yang berkualitas. Tidak ada salahnya jika anda mencoba bekerja sama dengan Spirit Konveksi. Dimana konveksi kami ini mampu memproduksi kaos dengan hasil memuaskan.
Untuk Info lebih lengkap silahkan hubungi admin kami di : 0822 2829 3811
klik logo whatsapp untuk live chat